
Transforming the drilling industry
Driving forward a step change in drilling performance, DualLink will transform the drilling industry. As the only wired drillpipe to leverage digital telemetry, power and greater reliability downhole, DualLink meets the needs of both land and offshore drilling.


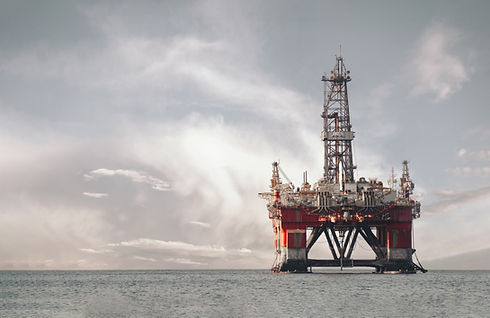


Benefits
DualLink re-defines the standard, enabling a step change in well construction to deliver predictable,
high-quality well construction.
By energizing the downhole BHA with data and power, DualLink’s benefits are three-fold:
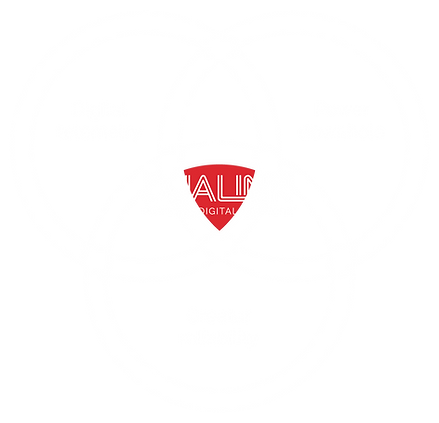

Data

More efficient drilling and less NPT
With high resolution downhole data and imagery enabling instant decision making.

Well placement quality improved
With high bandwidth logging and
drilling telemetry of 56 kb/s.

Enables drilling automation
Operates on an open platform; totally independent and can be integrated with any software or tools.
Power

500W of power at depth
Removes the need for downhole power sources for the BHA: shorter tools with measurements closer to the bit, less moving parts and lower asset and operating costs.

Environment and safety improved
Removes batteries from the BHA
and the associated handling,
transportation and disposal.
Reliability

Robust field replaceable connectors
Can be handled like an ordinary
drillpipe & easily integrates into
existing rig operations

Unique braided-cable design Provides >800 transmission channels to deliver greater surface contact and inbuilt redundancy.
Key selling points


Efficiency / environment
Improvement of 15%

Increase in total recovery by 20%*
*Source: Rystad Energy


DualLink is turning on the lights for downhole and bringing drilling out of the dark.
DualLink integrates easily into existing systems and can be handled in the same way as a regular drillpipe. Designed for the future, the technology enables shorter bottom hole assemblies (BHAs). The shorter BHA facilitates the design and use of lower cost tools and allows all measurements to be taken closer to the bit at much faster data rates.
DualLink is an efficient and robust engineered solution. Its future-proofed design results in a reduced risk of component failure.
The technology is also a more environmentally friendly option, as lithium batteries are no longer required, and faster drilling results in less rig emissions per well.
​
The potential of a powered drill string
-
Data challenge - Poor quality data results in low resolution downhole imaging, resulting in delayed decision making"With wired drillpipes, real time data from wells in any location can be presented and shared instantly, this facilitates real-time decision making at the rigsite and in town, and results in cost efficiencies.
-
Data challenge - Geosteering quality is limited, resulting in reduced production and recovery"By delivering high bandwidth logging and drilling telemetry of 56 kb/s, DualLink offers a real step change in visibility by supplying high-resolution real-time data & imagery. This means drilling decisions can be made instantly and accurately, without sacrificing drilling efficiencies to accurately place the wellbore in the optimal location.
-
Power challenge - A heavy reliance on inefficient solutions to deliver power downhole, such as litihium batteries or turbines downhole"By giving service companies power downhole from surface via the braid in the drillpipe, DualLink removes the need for batteries or turbines. Eventually, this will result in BHA tools without battery carriers or turbine assemblies: reducing BHA lengths and removing complexity.
-
Reliability challenge - No reliable method for high bandwidth communication downholeCurrent BHA to surface communications depend on 0.5-6bps (bits per second) mud-pulse or E-Mag communication technologies: not dis-similar to Morse Code bit rates. Acoustic technologies offer higher data rates in the 30-50bps range, but require repeaters and can suffer from drilling noise downhole. Downlinking to tools downhole requires flow rate or RPM adjustments or sometimes the dropping of RFID tags or balls into the drillstring. Wired pipe offers a 56,000bps high bandwidth bi-directional hardwire link between surface and downhole.
-
Reliability challenge - No comprehensive solution for drilling and rig automationThe industry is quickly developing and adopting automation technologies, both downhole and at surface. However, to deliver a fully closed loop system, we cannot rely on the low bit rate and high latency telemetry from current MWD (Measurement Whilst Drilling) technologies. High data rate, low latency, bi-directional communications is essential to finally deliver an automated drilling system. Developed as an open platform, DualLink is totally independent and can be integrated into any software and rig / BHA system.
-
Reliability challenge - Downhole tools have limited longevity - no integrated solutionDesign of the current BHA tool technologies require limited life batteries and rotating or pulsing mechanical devices to operate and send data uphole, both of which limit the operating envelope and longevity of tools and drilling runs. Wired pipe systems have also struggled with connector reliability challenges in the past. DualLink’s ability to send power via the drillpipe from surface to downhole removes the limitations and mechanical reliability concerns of downhole tools. The connector design of DualLink is robust, rig proven and field replaceable. DualLink can be treated like an ordinary drillpipe. Due to its open system, it easily integrates into a rig.
-
Reliability challenge - Drilling process is slow, labour intensive and inefficient"The introduction of the wired pipe moves the industry a step closer to an automated drill rig. This evolution will save time and money through fewer rig days and improve safety allowing experts to focus on value-add tasks and well control.
